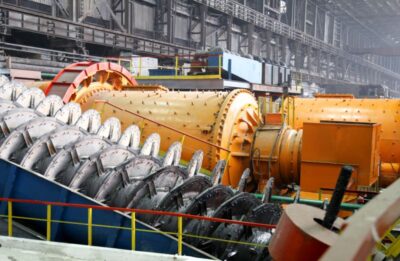
È risaputo che tutte le operazioni minerarie hanno un problema principale che non solo influisce sul funzionamento dell’impianto, ma soprattutto sul risultato finale: l’abrasione. Dal momento in cui il minerale inizia a essere movimentato con qualche metodo verso l’impianto di lavorazione, fino al momento in cui il prodotto finale viene gestito, ci sono attrezzature critiche che vengono affette dal fenomeno dell’abrasione . In alcune aree, le apparecchiature in esercizio possono richiedere la riparazione o la sostituzione anche ad intervalli settimanali, questo a causa dell’ambiente operativo aggressivo degli impianti minerari.
Prima di decidere come proteggere le apparecchiature dall’usura da azione abrasiva, è importante identificare i diversi tipi di meccanismi abrasivi, i quali portano in ogni caso tutti ad intaccare ed usurare le superfici delle apparecchiature:
Abrasione ad alta sollecitazione (“Three-Body abrasive wear”)
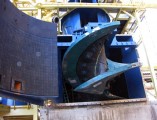
- Questo fenomeno si verifica in genere quando ci sono due superfici opposte in movimento relativo con particelle tra di esse. Se viene applicata una forza sulle particelle, si verifica una riduzione delle dimensioni ma anche una perdita di materiale dalle superficie reciprocanti.
- Questo tipo di abrasione si verifica tipicamente in apparecchiature come frantoi e mulini. La perdita di metallo in queste apparecchiature vitali per l’impianto influisce direttamente sulla resa e sulla produzione.
Abrasione da scorrimento a bassa sollecitazione (“Two-body abrasive wear”)
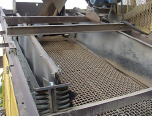
- In questo tipo di abrasione, di solito c’è una superficie statica con particelle che scorrono parallelamente ad essa. Questo processo agisce sulla superficie “graffiandola” e riducendone lo spessore.
- Questo tipo di meccanismo di usura interessa tipicamente le apparecchiature che gestiscono il movimento dei liquami e altre apparecchiature in cui le particelle si muovono sulla superficie. Le apparecchiature interessate comprendono pompe per liquidi e semisolidi, scivoli, agitatori e cicloni.
Abrasione da impatto
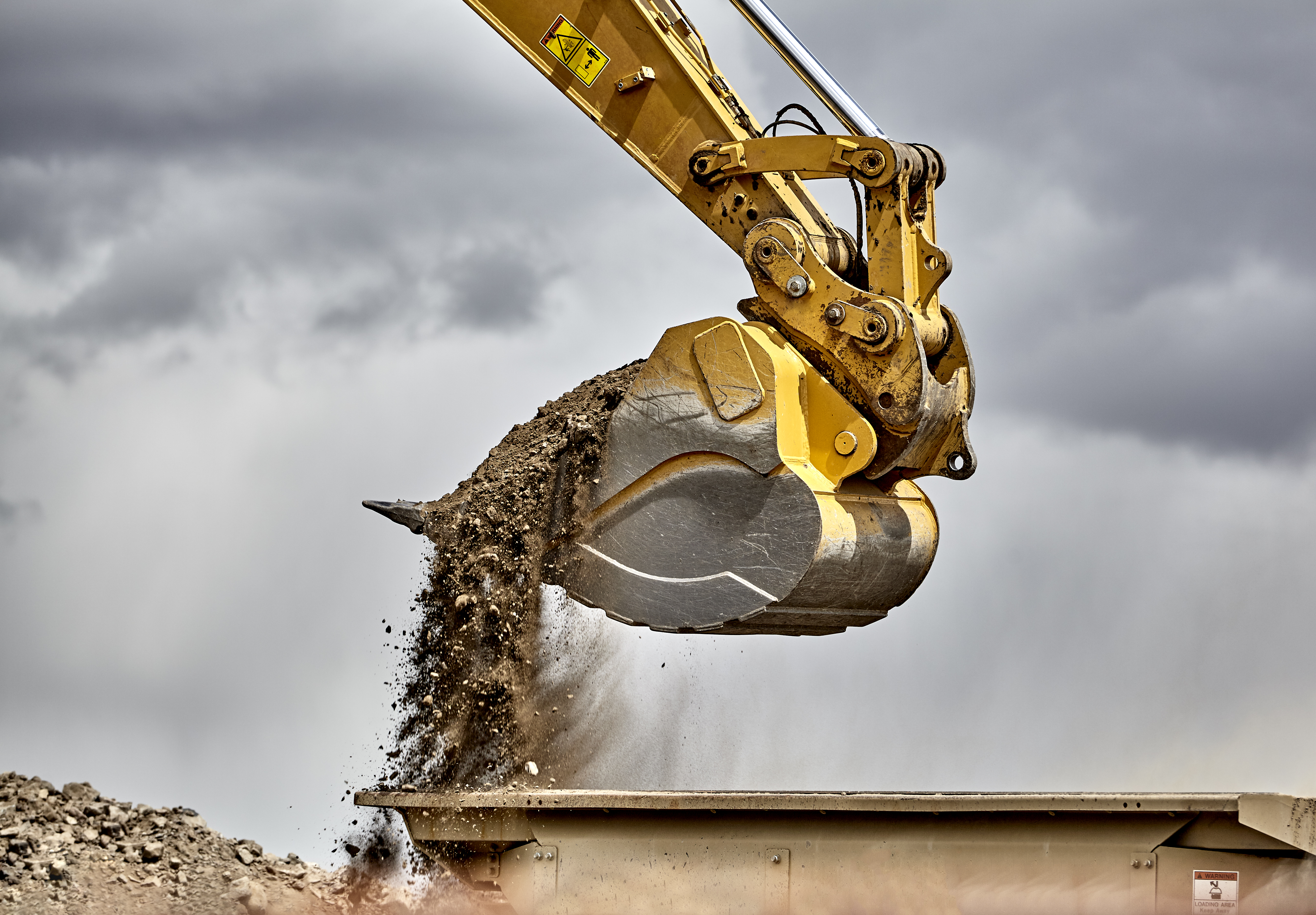
- Questo tipo di abrasione si verifica quando un flusso di particelle non scorre parallelamente alla superficie, ma viceversa impatta la stessa superficie con un angolo elevato, formando quindi piccole “craterizzazioni”.
- Con il passare del tempo, i substrati metallici possono subire una deformazione plastica che può anche portare a un cedimento per fatica. Questo meccanismo è comunemente riscontrato in attrezzature come le benne delle linee di trascinamento, gli escavatori e i frantoi.
L’aggressività e la gravità di un processo di abrasione dei sub-strati nelle situazioni precedentemente descritte, sono influenzate dai seguenti fattori:
- Durezza delle particelle: più le particelle sono dure, più grave è il meccanismo di abrasione.
- Forma delle particelle: le particelle di forma irregolare provocano un’abrasione più aggressiva rispetto alle particelle arrotondate.
- Densità delle particelle: influisce soprattutto sull’abrasione da impatto: maggiore è la densità, maggiore sarà l’energia da impatto in una superficie.
- Dimensione e peso delle particelle: le particelle più grandi o più pesanti comportano valori più elevati di perdita di metallo dal sub-strato.
- Velocità delle particelle: velocità più elevate delle particelle aumentano il grado di abrasione.
- Differenza di durezza tra le particelle e le superfici su cui agiscono: le particelle più dure producono una maggiore abrasione.
- Forza d’impatto: di solito è direttamente proporzionale all’altezza di caduta delle particelle su una superficie di usura.
- Percentuale di particelle solide nel liquame: maggiore è la percentuale di solidi, più il liquame è abrasivo.
- Portata fluidodinamica: con portate maggiori aumenta il livello di abrasione.
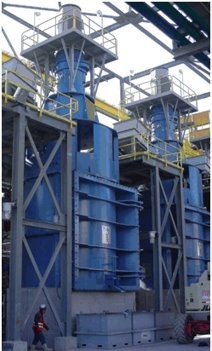
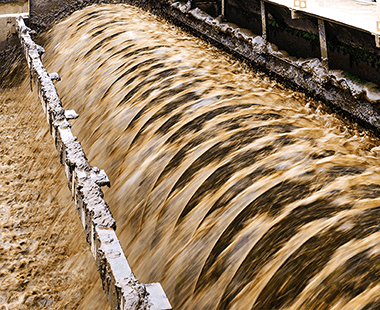
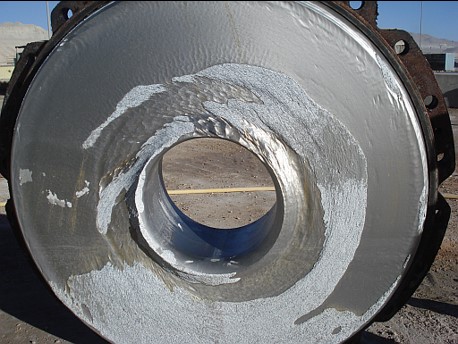
Vantaggi per il cliente nell’utilizzo di rivestimenti rinforzati con ceramica
Negli ultimi 30-35 anni, le tecnologie dei rivestimenti ceramici rinforzati sono state introdotte nel mercato industriale; le industrie minerarie e di lavorazione dei minerali hanno sempre più riconosciuto i potenziali vantaggi dell’uso di queste tecnologie per la protezione dall’abrasione delle apparecchiature di produzione più critiche.
Quali sono esattamente questi benefici e quali vantaggi presentano rispetto ai materiali tradizionali ed anche rispetto alle più recenti tecnologie di protezione dall’abrasione? Analizziamo:
- Come già affermato, l’abrasione è uno dei fattori che più influenzano la produzione nelle operazioni minerarie. L’investimento giornaliero per riparare/sostituire le attrezzature usurate rappresenta una parte consistente del budget totale per la manutenzione di qualsiasi operazione mineraria.
- I tempi di fermo della produzione sono un altro fattore estremamente importante. I fermi impianto non programmati di alcune apparecchiature di produzione nelle grandi miniere, possono comportare perdite di produzione pari a 50.000 dollari l’ora o anche di più.
- Disponibilità delle apparecchiature: questo punto si riferisce direttamente ai costi dei tempi di inattività, in quanto ogni volta che un’apparecchiatura richiede una riparazione deve essere fermata; pertanto, il settore è sempre alla ricerca di soluzioni più durature.
- La facilità della soluzione influisce anche sui tempi di fermo dell’apparecchiatura, poiché più tempo è necessario per implementare una soluzione resistente all’abrasione, maggiore è la perdita di produzione.
Prendendo in considerazione i fattori chiave descritti, possiamo metterli in relazione con i vantaggi che i rivestimenti ceramici offrono a questo settore:
- Sono la soluzione più conveniente per resistere alle condizioni di abrasione, se si considera il costo del rivestimento rispetto al tempo di fermo dell’apparecchiatura e alla durata della soluzione.
- Facile da applicare e può essere applicato in officina o direttamente dove si trova l’apparecchiatura , il che si traduce anche in minori perdite di tempo di fermo macchina.
- Possono essere facilmente adattati a qualsiasi forma della superficie e alla geometria dell’apparecchiatura.
- Possono essere utilizzati per riparare i rivestimenti tradizionali e le nuove tecnologie di protezione dall’abrasione, come i rivestimenti in gomma o le piastrelle in ceramica, risparmiando tempo rispetto alla rimozione di ampie aree di rivestimenti già installati.
- Hanno dimostrato prestazioni più durature rispetto alla gomma, alle leghe speciali e alle piastrelle in ceramica, anche in presenza di urti.
- Può essere facilmente riparato con ripristini localizzati, il che significa che il rivestimento rimanente, dopo un periodo di funzionamento, non deve essere rimosso ma solo pulito per accogliere il nuovo rivestimento.
- Possono aderire molto bene a diversi tipi di substrati, come tutti i tipi di metalli, gomma, piastrelle in ceramica e rivestimenti ceramici simili, dopo un’adeguata preparazione della superficie.
- Possono ridurre il magazzino dei pezzi di ricambio, poiché ora molti pezzi possono essere riparati più e più volte, purché siano strutturalmente sani.
- Vengono applicati senza bisogno di lavorazioni a caldo, il che migliora la sicurezza e significa anche che il substrato metallico non viene sottoposto allo stress indotto dal calore.
Questi vantaggi sono il motivo per cui l’industria mineraria e della lavorazione dei minerali utilizza rivestimenti rinforzati con ceramica per riparare, proteggere e rivestire le attrezzature esposte a condizioni abrasive.
Applicazioni comuni
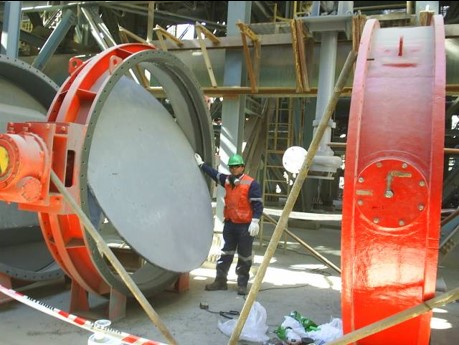
Questi rivestimenti rinforzati con ceramica sono utilizzati principalmente per proteggere le apparecchiature sottoposte all’abrasione da scorrimento a “due corpi” o in caso di deterioramento delle apparecchiature a causa di impatti. Possono essere utilizzati anche per proteggere apparecchiature soggette a corrosione chimica e a temperature elevate.
Alcune delle attrezzature ed apparecchiature più comuni nei siti minerari, in cui vengono utilizzati i rivestimenti ceramici rinforzati sono:
- Scivoli di carico e scarico
- Piastre di usura per nastri trasportatori
- Tramogge
- Cicloni
- Piastre di distribuzione dell’alimentazione del frantoio a cono secondario, terziario e quaternario
- Alimentatore a bocca del mulino a sfere
- Lamiere di scarico dei mulini a sfere e SAG (semi-autogeni) e rivestimenti a spirale
- Scatole di giunzione dello scarico del mulino
- Idrocicloni, camera di distribuzione, superfici interne, apice e canali di scarico
- Traverse del vaglio vibrante, aree di fuoriuscita materiale
- Pompe per i liquami di scarico del mulino a sfere; condotte di connessione per aspirazione e scarico e componenti interni
- Mulini verticali
- Rastrelliere, coni di scarico e gomiti per ispessitori di minerali e sterili
- Pompe per sterili, tubi e gomiti
- Pavimenti, troppo-pieno e filtri per celle di flottazione
- Scivolo di alimentazione e guscio dei tamburi di agglomerazione
- Sezioni di tubo e gomiti
- Corpi valvola, sedi ed elementi di tenuta
- Agitatori e pavimenti per serbatoi di liquami
- Trasportatori a coclea e canali
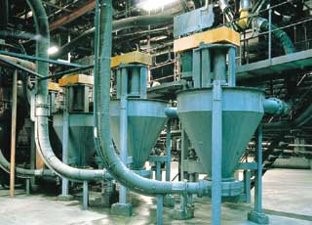
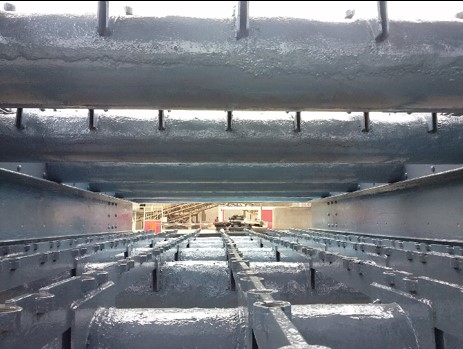
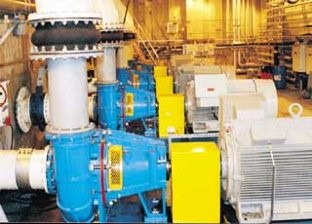
In conclusione, possiamo affermare che l’utilizzo dei rivestimenti ceramici rinforzati nelle attrezzature soggette ad abrasione abbia influenzato positivamente le pratiche di manutenzione nell’industria mineraria e della lavorazione dei minerali in tutto il mondo, grazie alla facilità d’uso, all’affidabilità, all’ottimizzazione dei costi e alle prestazioni garantite da questi materiali. Con lo sviluppo di nuove tecnologie, possiamo vedere che l’uso e la necessità di questi tipi di rivestimenti sono destinati a crescere e la necessità di sviluppare altri tipi di rivestimenti sarà decisa dalle esigenze del mercato in futuro.
Parlate con noi! Saremo lieti di offrirvi la soluzione di rivestimento ottimale. Rivolgetevi al nostro Expert Desk per ulteriori informazioni.
Potete anche effettuare una selezione preliminare utilizzando il nostro selettore di prodotti. I nostri consulenti di prodotto saranno lieti di assistervi nella scelta del prodotto ideale per la vostra applicazione.